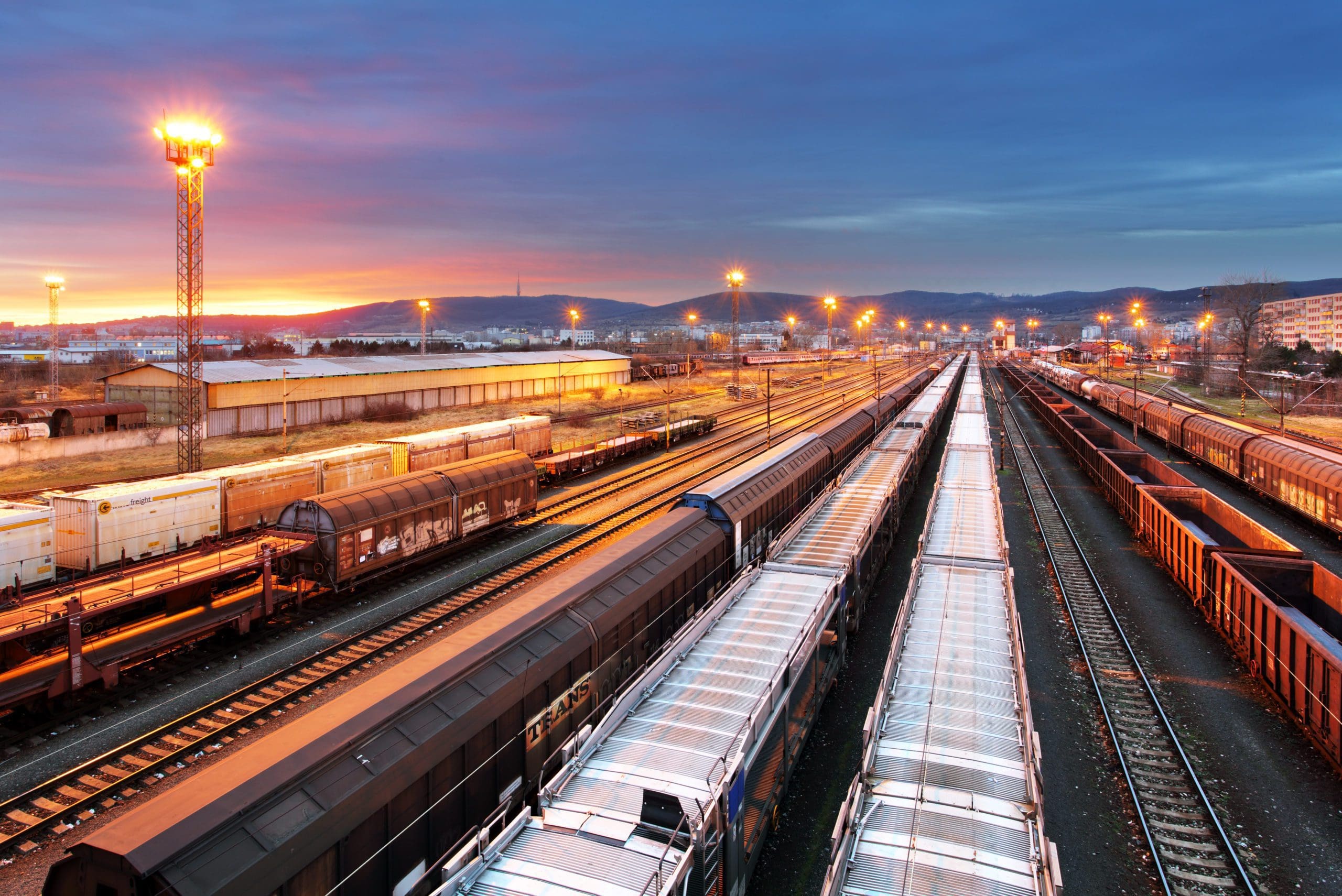
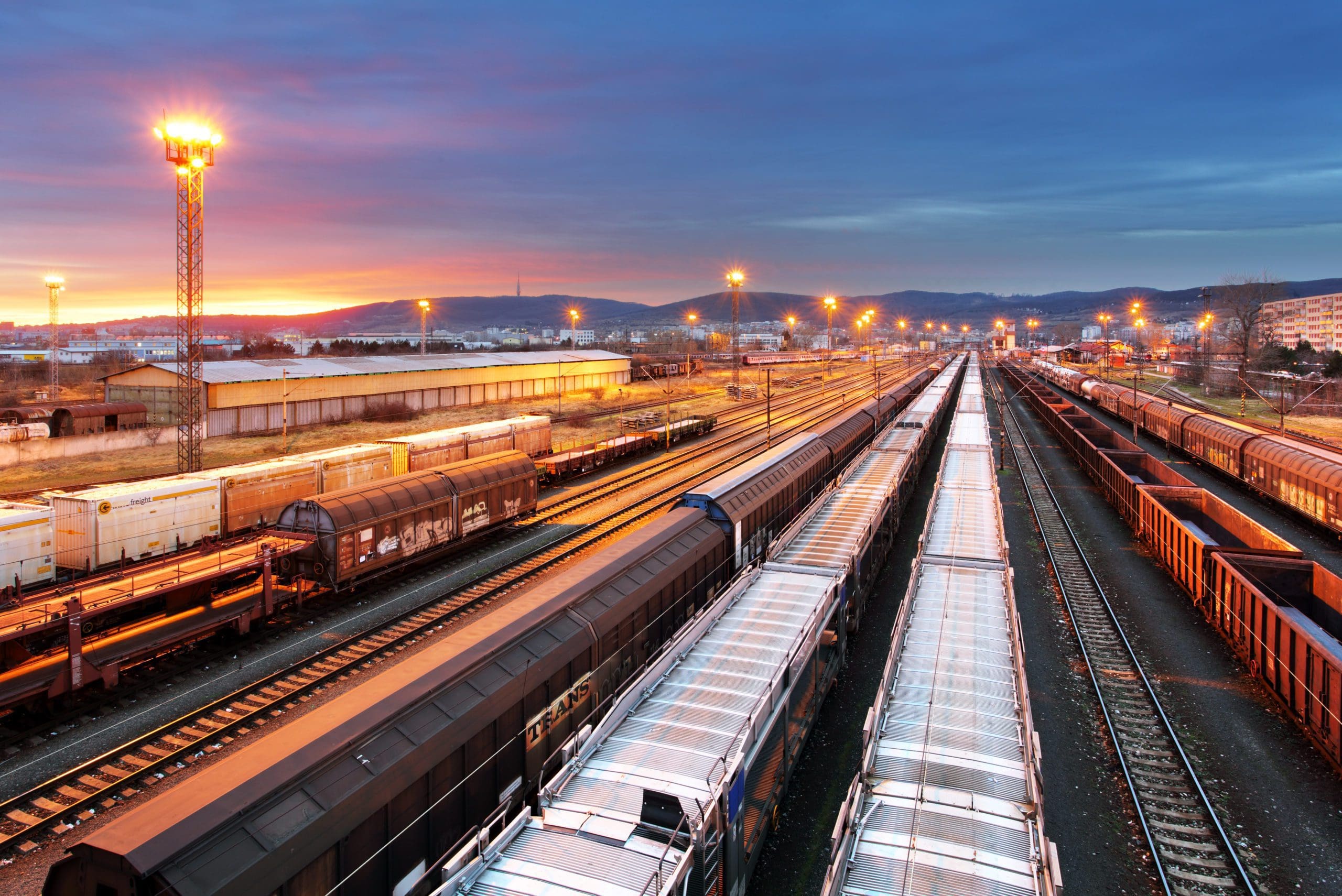
Rail grinding is a necessary maintenance process in the rail industry. Grinding happens in the field, but the technology back in the office also plays an important role.
ProRail is a public transport company that maintains the national rail infrastructure in the Netherlands. The company recently worked with Rizing on a new SAP implementation.
The result?
Powered by SAP, ProRail’s grinding process is now more efficient and accurate.
ProRail planners can react to track irregularities sooner, saving work hours in the office and on the ground. Before transforming the process with Rizing, a ProRail employee planned grinding jobs using an Excel spreadsheet. Turning around the work as fast as ProRail wanted was a challenge.
During a five-month project, Rizing helped ProRail define a new grinding policy, then design, build, test, and roll out an SAP-based solution.
Building on Linear Asset Data for Rail Grinding
SAP Linear Asset Management had previously been in place at ProRail, but it didn’t fully meet the need to create rail grinding plans. Specific rail characteristics for grinding and measuring points were missing in the system.
Planners can now create and assign required measuring points based on specific equipment and linear data.
We also helped ProRail clean up existing data and add data stored in systems outside of Linear Asset Management.
Staying Ahead of the Curve
With the new SAP solution, ProRail expects to schedule work orders for rail grinding two years ahead of when they expect to exceed the maximum allowed tonnage limits.
With the extra data, ProRail can now grind tracks and turnouts based on the asset’s condition instead of grinding strictly on timetables and regulations. They can even predict when grinding is necessary.
They’ll save money by grinding at the right time and place. This avoids unnecessary damage and maintenance on the track. Such a transformation in just five months is an incredible turnaround for both ProRail and Rizing.
Agile Process, Change Management Focus
ProRail and Rizing took an SAP Activate, agile approach to the rail grinding process. They kept business stakeholders involved by regularly demonstrating deliverables. The work was part of a broader change management strategy enabling transformation to take hold quickly.
ProRail provided workshops and training from the moment the implementation began—a significant step when making a dramatic transformation to a critical process.
Rizing provided extra workshops, training, and user manuals to ProRail when necessary.
Working together, ProRail, Rizing and SAP improved the ProRail grinding process, which will benefit the entire ProRail business.